Air Lift Pressure Sensor Fault; Everything You Need To Know.
The air lift pressure sensor is a revolutionary device that can measure the pressure of air and other gases in a variety of applications. It is designed to be rugged, reliable, and accurate, and can be used in a variety of industrial, commercial, and residential settings.
The air lift sensor has the ability to measure pressure in both positive and negative directions, allowing for precise and repeatable readings. It is also capable of detecting small pressure changes, making it an ideal choice for monitoring and controlling pressure in a variety of applications.
In some cases, the air lift pressure sensor fails and will need some repairing or replacement work. So in this article, you will learn everything you need to know about the air lift pressure sensor fault. Stick around until the end.
Table of Contents
- How does the airlift pressure sensor work?
- Causes of Air Lift Pressure Sensor Faults
- Troubleshooting Air Lift Pressure Sensor Fault.
- How to Prevent the Air Lift Pressure Sensor Faults?
- Some related FAQs.
How does the airlift pressure sensor work?
The airlift pressure sensor is used to detect the presence of liquid and/or gas in a vessel. It works by measuring the pressure in the vessel and converting it into an electrical signal.
The sensor is typically mounted near the bottom of the vessel, and it uses a diaphragm to measure the pressure inside. This diaphragm is connected to a pressure-sensitive switch that will open or close when the pressure inside the vessel changes.
When the switch is open, the signal is sent to the device that is associated with it, usually a controller or a monitoring system. The controller then interprets the signal and can take predetermined actions depending on the pressure reading.
How does the airlift pressure sensor work in cars?
The airlift pressure sensor works by detecting changes in the air pressure in the intake manifold of a vehicle’s engine. The sensor is typically mounted on the intake manifold and has a connection to a vacuum line.
As the engine’s RPM increases, the air pressure in the intake manifold increases. The sensor then sends a signal to the vehicle’s computer to adjust the fuel/air mixture accordingly. This helps to optimize engine performance and fuel efficiency.
Causes of Air Lift Pressure Sensor Faults
A. Poor Installation
Poor installation of the sensor can lead to a number of issues that can cause an Air Lift Pressure Sensor Fault. These issues include incorrect mounting of the sensor, incorrect wiring connections, or the use of incorrect electrical components.
All of these can lead to a malfunctioning sensor, which can cause inaccurate readings or failure to detect pressure changes. Additionally, incorrect calibration of the sensor can also cause Air Lift Pressure Sensor Faults.
B. Wrong Calibration
The wrong calibration of the air lift pressure sensor can cause the sensor to read inaccurate measurements. This can lead to false readings or the sensor failing to detect changes in pressure levels. This can cause the system to malfunction and result in incorrect readings or system failure.
C. Malfunctioning Components
The Malfunctioning Components of the sensor can cause air lift pressure sensor faults by causing inaccurate readings from the sensor. This can lead to inaccurate readings of pressure, which can cause the system to work improperly and lead to incorrect operation.
It can also lead to inaccurate pressure readings in the system, which can cause the system to malfunction or fail altogether. Malfunctioning components can also cause the sensor to overheat, which can lead to further damage or failure.
Troubleshooting Air Lift Pressure Sensor Fault.
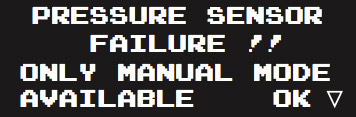
You have to troubleshoot the sensor when this failure message comes, and you may need an experienced mechanic for the job. But if you are able to do it alone, here is how to do it on your own.
A. Checking the Installation
- Check the mounting location for the pressure sensor: Make sure it is not too close to any other components that could cause interference.
- Check the air line: Make sure there are no blockages or leaks in the air line that could be causing the pressure to drop or rise too quickly.
- Check the air filter: Make sure the air filter is clean and not clogged with dust or debris.
B. Checking the Connections
- Check the wiring harness: Make sure all the wires are properly connected and that there are no frayed wires or open circuits.
- Check the ground connection: Make sure the ground is securely connected and that the ground wire is not damaged.
- Check the voltage: Make sure the voltage is within the acceptable range for your sensor.
C. Checking the Sensor Reading
To check the sensor reading of an air lift pressure sensor, first you need to identify the type of sensor you are using.
Depending on the type of sensor, the procedure to check the sensor reading may vary. For instance, if you are using a digital pressure sensor, you may need to connect the sensor to an external device, such as a computer or a handheld device, in order to read the sensor readings.
On the other hand, if you are using analog pressure sensors, you can use a multimeter to measure the voltage of the output signal from the sensor.
Once you have identified the type of sensor, you can then refer to the manufacturer’s instructions to check the sensor readings.
How to Prevent the Air Lift Pressure Sensor Faults?
1. Proper Installation:
Proper installation of an airlift pressure sensor is essential to ensure its proper operation and to minimize the risk of faults.
It is important to ensure that the airlift pressure sensor is installed in the correct position, with the correct orientation, and with the correct fittings.
Additionally, the airlift pressure sensor should be mounted securely to a stable surface and be away from any sources of vibration or extreme temperatures.
2. Regular Maintenance:
Regular maintenance of the air lift pressure sensor is also necessary to ensure its proper operation and to prevent faults. This includes regularly inspecting the sensor for any signs of damage or wear, and ensuring that the connections are tight and secure.
Any damage should be repaired or replaced as soon as possible. Additionally, the air lift pressure sensor should be regularly calibrated to ensure that it is providing accurate readings.
3. Proper Calibration:
Proper calibration of the air lift pressure sensor is essential for its proper operation and to prevent faults. Calibration should be done using a certified calibrator and should include both zero and span calibration.
Additionally, the calibration interval should be established based on the system requirements, and the calibration should be regularly verified to ensure that the sensor is providing accurate readings.
ABS Light Still On After Sensor Replacement; What You Should Do?
Sensor diary
Some related FAQs.
How to reset the air lift controller?
Until the displayed number begins blinking, press and hold the M button and the Number button for one to three seconds. To adjust to the height saved at that number, press and hold the desired Number button twice. – – – Reset
How do you calibrate an Airlift 3H?
You must simultaneously press the top and middle Air Lift buttons to calibrate your 3P or 3H management system. Then, descend and select “Calibration,” adhere to the prompts on the screen, and let the process finish.